Electroplating
Key Notes :
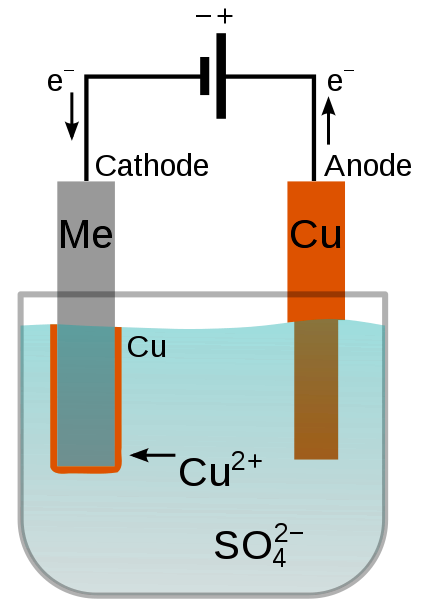
Definition of Electroplating:
- Electroplating is a process of coating a thin layer of metal onto another metal using an electric current. This is done to improve the appearance, durability, or resistance of the metal object.
How Electroplating Works:
- In electroplating, the object to be plated (cathode) is connected to the negative terminal of a power supply.
- The metal that will coat the object (anode) is connected to the positive terminal.
- Both the object and the metal are placed in a solution containing a salt of the metal to be plated.
- When electricity passes through the solution, metal ions are transferred from the anode to the cathode, forming a thin metal layer.
Common Uses of Electroplating:
- Decorative purposes: Jewelry, cutlery, and coins are electroplated to give them a shiny, appealing finish (e.g., silver or gold plating).
- Corrosion resistance: Metals like iron are electroplated with zinc (galvanization) to prevent rusting.
- Wear resistance: Tools and machinery parts are plated with harder metals (like chromium) to reduce wear and tear.
- Improving electrical conductivity: Copper or silver plating is done to improve the conductivity of electrical components.
Examples of Electroplating:
- Gold-plated jewelry.
- Chrome plating on car bumpers.
- Zinc coating on steel for corrosion resistance (galvanization).
Advantages of Electroplating:
- Enhances the appearance of objects by giving them a polished, shiny finish.
- Protects metals from corrosion and rust.
- Increases the hardness and durability of materials.
- Improves electrical conductivity in electronic components.
Disadvantages of Electroplating:
- It requires careful handling of chemicals, which can be hazardous.
- The process can be expensive depending on the materials used.
- Disposal of waste chemicals may cause environmental harm if not managed properly.
Electroplating vs. Galvanization:
- Electroplating is a more controlled process, while galvanization usually refers to coating steel with zinc to prevent rust.
Let’s practice!